Verfahren und Konzept für Ammoniakanlagen von Uhde basieren auf zuverlässigen und bewährten Prozessschritten. Die wichtigsten Merkmale sind ein deckenbefeuerter Primärreformer mit einem Kaltauslass-Verteilersystem, ein Sekundärreformer mit einem Umlauf-Wirbelbrenner und drei Katalysatorbetten auf Magnetitbasis nach dem Radialflussprinzip zur Wärmeaustauschsynthese mit einem oder zwei Synthesekonvertern.
Der Rohstoff (beispielsweise Erdgas) wird entschwefelt, mit Dampf vermischt und mit Nickelkatalysatoren bei etwa 40 bar und 800°C im Primärreformer in Synthesegas umgewandelt. Der Dampfreformer von Uhde ist ein deckenbefeuerter Reformer mit Rohren aus einem im Schleudergussverfahren hergestellten legierten Stahl und einem urheberrechtlich geschützten Kaltauslass-Verteilersystem zur Verbesserung der Zuverlässigkeit.
Das Prozessgas, das den Primärreformer verlässt, gelangt in den Sekundärreformer, wo dem Synthesegas über ein spezielles Düsensystem, das für eine perfekte Mischung aus Luft und Gas sorgt, Prozessluft zugeführt wird. Die folgende Hochdruck-Dampferzeugung und Überhitzung ermöglichen eine maximale Prozesswärmenutzung, wodurch eine optimale Energieeffizienz erreicht wird. Seit seiner Einführung im Jahre 1968 hat sich der Sekundärreformer von Uhde als zuverlässiges Gerät mit langer Lebensdauer erwiesen.
Kohlenmonoxid wird in der HT- und LT-Schicht über Standardkatalysatoren zu Kohlendioxid umgewandelt. Kohlendioxid wird in einer Abluftreinigungsanlage entfernt, bei der üblicherweise das BASF-OASE- oder das UOP-Benfield-Verfahren zum Einsatz kommt. Verbleibende Kohlenoxide werden durch katalytische Methanisierung im ppm-Spurenbereich zu Methan rückkonvertiert.
Das Ablaufdiagramm einer Uhde-Ammoniakanlage zeigt die herkömmliche Reihenfolge der Prozessschritte, die die Basis der meisten heutzutage angewandten Ammoniakverfahren bilden. Eine genauere Überprüfung der Fakten und Zahlen zeigt jedoch, dass das, was eine konventionelle Aufstellung zu sein scheint, tatsächlich ein hochmodernes Ammoniakanlagenkonzept ist. Der Gesamtverbrauch (Rohstoff + Treibstoff + Strom) pro Tonne hergestellten Ammoniaks liegt im Bereich zwischen 6,6 bis 7,2 Gcal (27,6 bis 30,1 GJ), je nach örtlichen Gegebenheiten (z. B. Temperatur des Kühlwassers) und projektspezifischen Anforderungen (wie beispielsweise Erdgaspreis usw.).
In folgenden Prozessbereichen wurden wesentliche Änderungen vorgenommen, um diese Werte zu erzielen:
- Dampfreformierungsanlage einschließlich Abwärmerückgewinnungssystem;
- CO2-Abscheidungsanlage;
- Ammoniaksyntheseanlage.
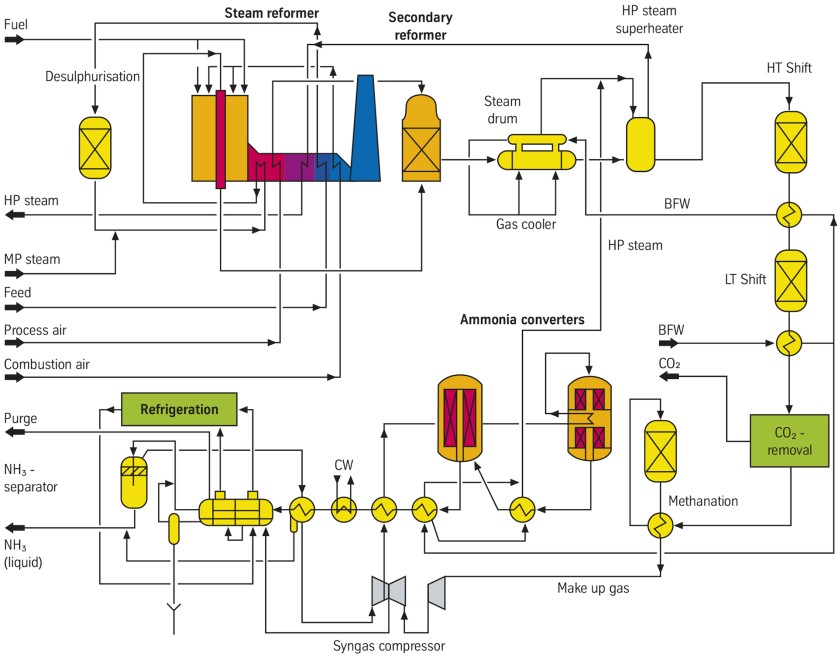