The chemical and fertilizer industries have relied upon large-scale ammonia plants during the past four dec-ades because economies of scale favor the lower specific construction and production costs.
The business model for these larger plants was partly based on the fact that the ammonia product not consumed on-site could be exported, calling for straightforward transportation to other users at economically attractive costs. However, increasing safety and security concerns for transporting hazardous chemicals have led to higher freight rates and insurance premiums for the transportation of anhydrous ammonia. This affects most small-scale ammonia consumers who depend on importing ammonia by rail, barge or road.
A viable alternative is to co-locate a small-scale ammonia production facility with a consuming facility and thus to eliminate the transport risk and costs. Conventional plant designs face technical and economic chal-lenges below plant capacities of 600 short tons per day (550 metric tons per day). thyssenkrupp Industrial Solutions and Johnson Matthey have addressed this concern, developing an economic concept for smaller plants based on gas heated reformer technology.
As a consequence, thyssenkrupp Industrial Solutions can now offer a plant capacity range of 270 to 550 met-ric tons per day (300 to 600 short tons per day) and has a standard design of 360 short tons per day available and ready to go. This plant uses a gas heated reformer (GHR) and a pressure swing adsorption (PSA) sys-tem in the front end and an Uhde low pressure synthesis loop in the back end.
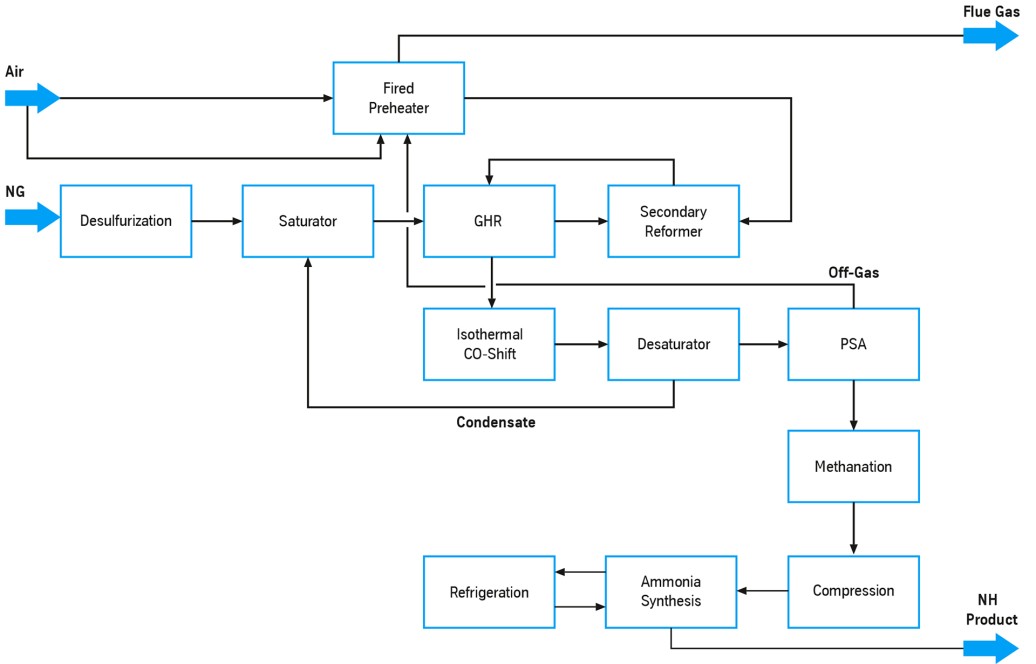